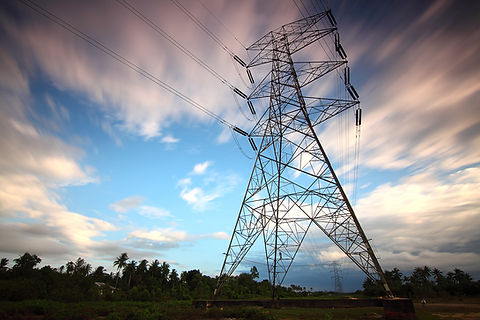
MAINTENANCE
Routine electrical maintenance provides a pro-active solution in the prevention of many unforeseen breakdowns, provides a window for various repair works to be completed, and is also paramount in ensuring the electrical apparatus installed reaches its full operating life cycle as outlined by manufacturers.
​
Our maintenance services include but are not limited to Switchboard maintenance, Power Factor Correction Maintenance and Thermal Imaging.
​
"Why wait for a breakdown, implement a pro-active solution"

Switchboard maintenance
Providing conditional and periodic maintenance solutions tailored to your sites requirements.
​
-
Main Switchboards, Distribution Boards, Mechanical Distribution Boards.
-
Physical Maintenance: Clean, random torque tension, sealing of penetrations, clearances.
-
Equipment: Physical operation & condition, trip unit testing (as required), interlocks, function.
-
Air Circuit Breakers: Physical operation & condition, trip unit testing (as required), interlocks, function.
-
Moulded Case Circuit Breakers: Physical operation & condition, trip unit testing (as required), interlocks, function.
-
Automatic Transfer Units: Physical operation & condition, trip unit testing (as required), interlocks, mains fail simulation and transfer simulation (as required).
-
Detailed report issued on completion.

PFC TESTING & MAINTENANCE
Ensure your Power Factor Correction Unit is working at optimum efficiency while also increasing its operating life cycle.
​
-
Control equipment operation (Controller, contactors, thermostat etc.)
-
Unit operation: Auto & Manual (Individual step engagement).
-
Capacitor testing: Confirmation of load readings to manufacturers recommended thresholds.
-
Confirmation of current transformer settings.
-
Physical Maintenance: Internal & external clean, torque tension on electrical terminations, clearances, cable glanding and bushing, fixing and supports.
-
Thermal scan included
-
Detailed report issued on completion, including recommendation, rectifications & budgets.

THERMAL IMAGING
A form of non-intrusive preventative maintenance, providing a form of risk mitigation against fire, electrical and safety hazards.
​
-
Scanning of electrical equipment identifying sources of abnormal thermal radiation "Hot Spots".
-
Pro-active method in determining risks before its to late.
-
Fully calibrated thermal camera's used by experienced and trained staff.
-
Comprehensive report issued on completion.
​
For even greater risk mitigation combine thermal imaging with our condition and compliance inspection.

RCD TESTING
Ensure your RCD's operating parameters are tested and comply with the relevant Australian Standards and Safe Work Australia.
​
-
Testing & Compliance to AS/NZS 3017:2007
-
Pushbutton Testing, Trip Time Testing (0 & 180) & Trip Current Testing
-
Testing using fully calibrated tester (Megger MFT1835 - pictured)
-
Testing completed using trained and qualified personnel
-
Report produced documenting all results for tested RCDs
​